Technion Wind-tunnel Complex (TWTC) recently commissioned an operating Hypersonic Ludwieg Tunnel (HLT) on 11th October 2021. Ludwieg tunnels are short-duration high-speed facilities. A long tube containing the high-pressure gas, and a model kept at a very low vacuum pressure are separated by a diaphragm or fast-acting valve. A typical layout of the experimental facility along with the optical diagnostics (a. schlieren, and b. laser Rayleigh scattering) is shown in the figure below. The Ludwieg tube is 3 m long and 22 mm in diameter (inner). The tube is arranged in a ‘U’-tube configuration to save some floor space. The tube is wrapped by heater pads which can maintain a surface temperature of up to 500 K. At one end of the tube, a commercial fast-acting valve (ISTA® KB-20-10) with a valve opening time of <1 ms is connected. The tube can be pressurized to the desired fill pressure ranging between 3 to 10 bar, by using the ports in the fast-acting valve itself. Computer-controlled pneumatic actuators and pressure regulators operate the fast-acting valve. During the fast-acting valve operation, there is a total pressure drop of about 20%. Hence, a small tube is connected after the valve to measure the actual flow stagnation properties. A convergent-divergent (C-D) nozzle is attached next, whose interior is mirror-polished to have a smooth wall surface with a roughness radius of about 0.1 μm. The nozzle is designed to produce an exit Mach number of 6.0. However, after manufacturing, the nozzle’s divergent section is measured to have a semi-cone angle of 7∘ with a throat and exit diameter of 10.4 mm and 76.2 mm, resulting in an actual exit Mach number of 6.01. The nozzle expands freely into a closed chamber of volume 0.1 cubic meter and 0.5 m long. The chamber also possesses four hermetically sealed optical windows (each 100 mm in diameter) closer to the nozzle exit section and wiring ports for instrumentation downstream. The chamber can be kept to a vacuum level of 0.05 mbar using a rotary vacuum pump (Busch® RH0021B-Zebra) while monitoring the vacuum pressure level. At the nozzle exit, the unit freestream Reynolds number is changed by varying the total pressure in the Ludwieg tube. A wide range of Reynolds numbers (4.75 million to 18 million) is achieved while changing the total pressure between 3 to 10 bar with dry air as the test gas. The tunnel is fully automated and operated autonomously for safety and efficiency. The NI (National Instruments)-based multi-functional I/O data card monitors the necessary pressure ratio between the vacuum tank and the Ludwieg tube. Once the desired value is reached, a trigger is sent to actuate the fast-acting valve to initiate the flow. After extensive calibration, the stationary flow time is estimated to be 12.5 ms and the effective model diameter is found to be 40 mm.
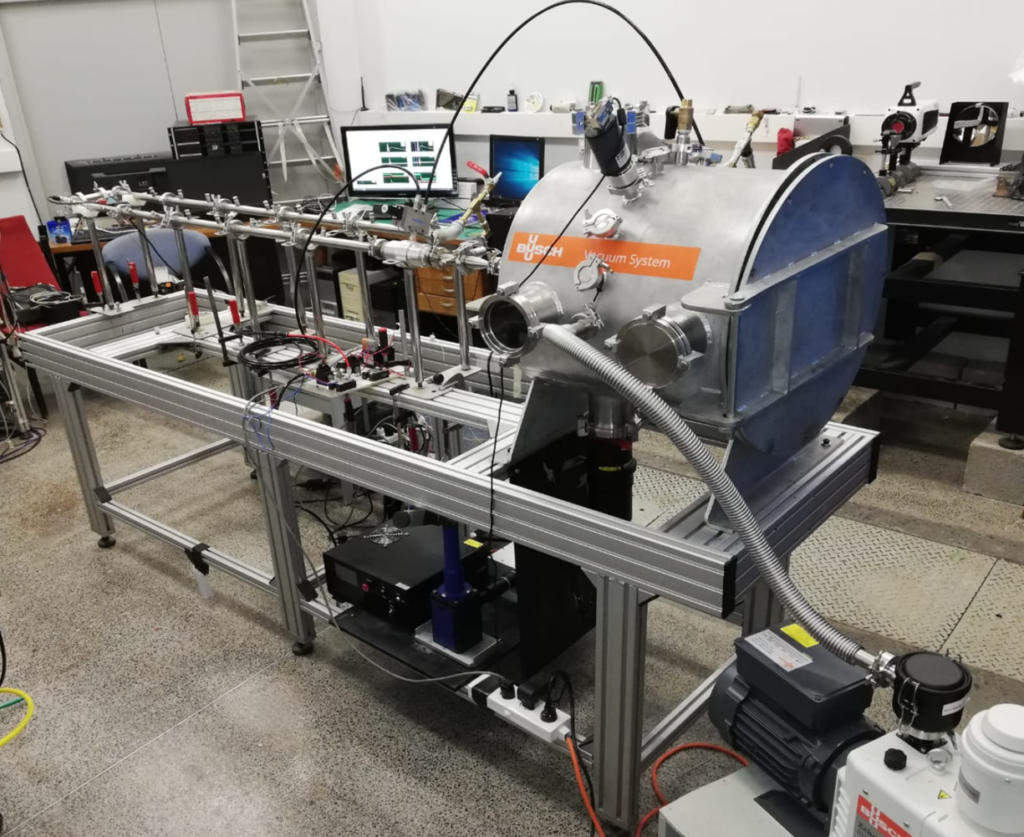
More details about the facility are available at: https://doi.org/10.1007/s00348-022-03559-7
Karthick, S.K., Nanda, S.R. & Cohen, J. Unsteadiness in hypersonic leading-edge separation. Exp Fluids 64, 13 (2023).